|
|
(178 intermediate revisions by 16 users not shown) |
Line 1: |
Line 1: |
− | <div id="PageBody"><div id="PageContent">
| + | [[Portal:Biogas|►Back to Biogas Portal]] |
− | = Biogas - Digester types =
| |
| | | |
− | In this chapter, the most important types of biogas plants are described:
| + | = Introduction = |
| | | |
− | *'''Fixed-dome plants'''
| + | {| cellpadding="5" border="0" align="right" style="width: 309px;" |
− | *'''Floating-drum plants'''
| + | |- |
− | *'''Low-Cost Polyethylene Tube Digester'''<br>
| + | | style="width: 250px;" | |
− | *'''Balloon plants'''
| + | [[File:Digestneck.jpg|278px|RTENOTITLE]] |
− | *'''Horizontal plants'''
| |
− | *'''Earth-pit plants'''
| |
− | *'''Ferrocement plants'''
| |
− | *[[ARTI Biogas Plant|'''ARTI Biogas Plant''']]
| |
| | | |
− | <br> | + | '''Construction of the digester neck with steel reinforcement'''<ref name="Photo: Krämer (TBW)">Photo: Krämer (TBW)</ref><br/> |
| | | |
− | Of these, the two most familiar types in developing countries are the '''fixed-dome plants''' and the '''floating-drum''' plants. Typical [[Types of Biogas Digesters and Plants#Digester_types_in_industrialized_countries|designs in industrialized countries]] and [[Types of Biogas Digesters and Plants#Selection_of_appropriate_design|appropriate design selection criteria]] have also been considered.
| + | |} |
| | | |
− | == Fixed-dome plants ==
| + | Choosing a right biogas digester is a very important while constructing a biogas plant. From the standpoint of fluid dynamics and structural strength, an egg-shaped vessel is about the best possible solution. This type of construction, however, is comparatively expensive, therefore, its use is usually restricted to large-scale sewage treatment plants. The Chinese [[Fixed-dome_Biogas_Plants|fixed-dome]] designs are of similar shape, but less expensive. The hemispherical CAMARTEC design is optimized in structural strength, but does not make optimal use of the excavation required. |
| | | |
− | The costs of a fixed-dome biogas plant are relatively low. It is simple as no moving parts exist. There are also no rusting steel parts and hence a long life of the plant (20 years or more) can be expected. The plant is constructed underground, protecting it from physical damage and saving space. While the underground digester is protected from low temperatures at night and during cold seasons, sunshine and warm seasons take longer to heat up the digester. No day/night fluctuations of temperature in the digester positively influence the bacteriological processes.
| + | Simplified versions of such digester designs include cylinders with conical covers and bottoms. They are much easier to build and are sometimes available on the market as prefabricated units. Their disadvantage lies in their less favorable surface-volume ratio. The cylinder should have a height equal to its diameter. ''Prone cylinders'' have become quite popular on farms, since they are frequently the more favorable solution for small-scale bio-methanation. ''Cuboid digesters'' are often employed in batch-fed systems used primarily for fermenting solid material, so that fluid dynamics are of little interest. |
| | | |
− | The construction of fixed dome plants is labor-intensive, thus creating local employment. Fixed-dome plants are not easy to build. They should only be built where construction can be supervised by experienced biogas technicians. Otherwise plants may not be gas-tight (porosity and cracks).
| |
| | | |
− | The basic elements of a fixed dome plant (here the '''Nicarao Design''') are shown in the figure below.
| + | = Types of Small-Scale Digesters = |
| | | |
− | {| cellspacing="0" cellpadding="0" border="0"
| + | == Fixed Dome Biogas Plants == |
− | |-
| + | A fixed-dome plant comprises of a closed, dome-shaped digester with an immovable, rigid gas-holder and a displacement pit, also named 'compensation tank'. The gas is stored in the upper part of the digester. When gas production commences, the slurry is displaced into the compensating tank. Gas pressure increases with the volume of gas stored, i.e. with the height difference between the two slurry levels. If there is little gas in the gas-holder, the gas pressure is low.<br/> |
− | | width="45%" | <br>
| |
− | | [[Image:Nicarao biogas.gif]] <small class="IMGLEGEND">''''''Fixed dome plant Nicarao design''': 1. Mixing tank with inlet pipe and sand trap. 2. Digester. 3. Compensation and removal tank. 4. Gasholder. 5. Gaspipe. 6. Entry hatch, with gastight seal. 7. Accumulation of thick sludge. 8. Outlet pipe. 9. Reference level. 10. Supernatant scum, broken up by varying level.'''<br> </small><small class="IMGSOURCE">''Source: TBW''</small>
| |
− | | width="45%" | <br>
| |
− | |}
| |
| | | |
− | {| cellpadding="10" border="0" align="left" style="width: 397px; height: 472px;" class="IMGright"
| + | [[Fixed-dome Biogas Plants#Fixed-dome Plants|►Read more here...]] |
− | |-
| |
− | | [[Image:Fixdomscheme.gif]] <small class="IMGLEGEND">'''Basic function of a fixed-dome biogas plant, 1 Mixing pit, 2 Digester, 3 Gasholder, 4 Displacement pit, 5 Gas pipe'''<br> </small><small class="IMGSOURCE">''Source: OEKOTOP''</small> <br> | |
− | |}
| |
| | | |
− | <br>
| |
| | | |
− | === Function === | + | == Floating Drum Plants == |
| + | Floating-drum plants consist of an underground digester and a moving gas-holder. The gas-holder floats either directly on the fermentation slurry or in a water jacket of its own. The gas is collected in the gas drum, which rises or moves down, according to the amount of gas stored. |
| | | |
− | A fixed-dome plant comprises of a closed, dome-shaped digester with an immovable, rigid gas-holder and a displacement pit, also named 'compensation tank'. The gas is stored in the upper part of the digester. When gas production commences, the slurry is displaced into the compensating tank. Gas pressure increases with the volume of gas stored, i.e. with the height difference between the two slurry levels. If there is little gas in the gas-holder, the gas pressure is low. <br><br>
| + | [[Floating Drum Biogas Plants|►Read more here...]] |
| | | |
− | === Digester ===
| |
| | | |
− | The digesters of fixed-dome plants are usually masonry structures, structures of cement and ferro-cement exist. Main parameters for the choice of material are:
| |
| | | |
− | *Technical suitability (stability, gas- and liquid tightness);
| + | == Low-Cost Polyethylene Tube Digester == |
− | *cost-effectiveness;
| |
− | *availability in the region and transport costs;
| |
− | *availability of local skills for working with the particular building material.
| |
| | | |
− | Fixed dome plants produce just as much gas as floating-drum plants, ''if they are gas-tight''. However, utilization of the gas is less effective as the gas pressure fluctuates substantially. Burners and other simple appliances cannot be set in an optimal way. If the gas is required at constant pressure (e.g., for engines), a gas pressure regulator or a floating gas-holder is necessary.
| + | The Low-Cost Polyethylene Tube Digester model consist of tubular polyethylene film (two coats of 300 microns) bent at each end around a 6 inch PVC drainpipe and is wound with rubber strap of recycled tire-tubes. |
| | | |
− | {| cellpadding="10" border="0" align="right" style="width: 366px; height: 333px;"
| + | [[Low-Cost_Polyethylene_Tube_Digester|►Read more here....]] |
− | |-
| |
− | | | |
− | <small class="IMGLEGEND">'''[[Image:Biogastunesia01.jpg]]'''</small>
| |
| | | |
− | <small class="IMGLEGEND">'''Fixed-dome plant in Tunesia. The final layers of the masonry structure are being fixed.'''<br> </small><small class="IMGSOURCE">''Photo: gtz/GATE''</small>
| |
| | | |
− | |}
| |
| | | |
− | <br><br><br>
| + | == Balloon Plants == |
| | | |
− | === Gas-Holder ===
| + | A balloon plant consists of a heat-sealed plastic or rubber bag (balloon), combining digester and gas-holder. The gas is stored in the upper part of the balloon. The inlet and outlet are attached directly to the skin of the balloon.<br/>[[Balloon_Digester_for_Biogas_Plants|►Read more here...]] |
| | | |
− | The top part of a fixed-dome plant (the gas space) must be gas-tight. Concrete, masonry and cement rendering are not gas-tight. The gas space must therefore be painted with a [[Plasters and coats for digesters and gas-holder|gas-tight layer]] (e.g. 'Water-proofer', Latex or synthetic paints). A possibility to reduce the risk of cracking of the gas-holder consists in the construction of a [[Optional Parts of a biogas plant#Weak_ring|weak-ring]] in the masonry of the digester. This "ring" is a flexible joint between the lower (water-proof) and the upper (gas-proof) part of the hemispherical structure. It prevents cracks that develop due to the hydrostatic pressure in the lower parts to move into the upper parts of the gas-holder.
| |
| | | |
− | <br><br><br><br><br><br><br> | + | == Horizontal Plants<br/> == |
| | | |
− | === Types of fixed-dome plants ===
| + | Disadvantages''': Problems with gas-space leakage, difficult elimination of scum.'''<br/> |
| | | |
− | {| width="259" cellpadding="10" border="0" align="right" class="IMGright"
| + | [[#toc|►Go to Top]]<br/> |
− | |-
| |
− | | <small class="IMGLEGEND">'''Chinese fixed dome plant'''<br> </small><small class="IMGSOURCE">''Source: TBW''</small> <br>
| |
− | |}
| |
| | | |
− | *'''Chinese fixed-dome plant''' is the archetype of all fixed dome plants. Several million have been constructed in [[Biogas technology in China (Sichuan)|China]]. The digester consists of a cylinder with round bottom and top.
| |
− | *'''Janata model '''was the first fixed-dome design in [[Biogas technology in India|India]], as a response to the Chinese fixed dome plant. It is not constructed anymore. The mode of construction lead to cracks in the gasholder - very few of these plant had been gas-tight.
| |
− | *'''Deenbandhu,''' the successor of the Janata plant in India, with improved design, was more crack-proof and consumed less building material than the Janata plant. with a hemisphere digester
| |
− | *'''CAMARTEC model''' has a simplified structure of a hemispherical dome shell based on a rigid foundation ring only and a calculated joint of fraction, the so-called weak / strong ring. It[[Image:Chinafixdome.gif]] was developed in the late 80s in [[Biogas technology in Tanzania|Tanzania]].
| |
| | | |
− | <br> | + | == Earth-pit Plants<br/> == |
| | | |
− | <br>
| + | Masonry digesters are not necessary in stable soil (e.g. laterite). It is sufficient to line the pit with a thin layer of cement (wire-mesh fixed to the pit wall and plastered) in order to prevent seepage. The edge of the pit is reinforced with a ring of masonry that also serves as anchorage for the gas-holder. The gas-holder can be made of metal or plastic sheeting. If plastic sheeting is used, it must be attached to a quadratic wooden frame that extends down into the slurry and is anchored in place to counter its buoyancy. The requisite gas pressure is achieved by placing weights on the gas-holder. An overflow point in the peripheral wall serves as the slurry outlet'''. |
| | | |
− | {| cellspacing="0" cellpadding="0" border="0" class="IMGcenter"
| |
− | |-
| |
− | | width="45%" | <br>
| |
− | | [[Image:Camartecfixdome.gif]]<small class="IMGLEGEND">'''Fixed dome plant CAMARTEC design'''<br> </small><small class="IMGSOURCE">''Source: TBW''</small>
| |
− | | width="45%" | <br>
| |
− | |}
| |
| | | |
− | <br>
| + | '''Advantages''' |
| + | *Low cost of installation (as little as 20% of a floating-drum plant); |
| + | *high potential for self help approaches. |
| | | |
− | === Climate and size ===
| |
| | | |
− | Fixed-dome plants must be covered with earth up to the top of the gas-filled space to counteract the internal pressure (up to 0,15 bar). The earth cover insulation and the option for internal heating makes them suitable for colder climates. Due to economic parameters, the recommended minimum size of a fixed-dome plant is 5 m<sup>3</sup>. Digester volumes up to 200 m<sup>3</sup> are known and possible.
| + | '''Disadvantages''' |
| + | *Short useful life; serviceable only in suitable, impermeable types of soil. |
| + | *Earth-pit plants can only be recommended for installation in impermeable soil located above the groundwater table. Their construction is particularly inexpensive in connection with plastic sheet gas-holders. |
| | | |
− | '''''Advantages:''''' Low initial costs and long useful life-span; no moving or rusting parts involved; basic design is compact, saves space and is well insulated; construction creates local employment.
| + | <br/> |
| | | |
− | '''''Disadvantages:''''' Masonry gas-holders require special sealants and high technical skills for gas-tight construction; gas leaks occur quite frequently; fluctuating gas pressure complicates gas utilization; amount of gas produced is not immediately visible, plant operation not readily understandable; fixed dome plants need exact planning of levels; excavation can be difficult and expensive in bedrock. </div>
| + | [[Fixed-dome_Biogas_Plants#toc|►Go to Top]]<br/> |
| | | |
− | Fixed dome plants can be recommended only where construction can be supervised by experienced biogas technicians.
| + | == Ferro-cement Plants == |
| | | |
− | <br> | + | The ferro-cement type of construction can be applied either as a self-supporting shell or an earth-pit lining. The vessel is usually cylindrical. Very small plants (Volume under 6 m<sup>3</sup>) can be prefabricated. As in the case of a fixed-dome plant, the ferrocement gasholder requires special sealing measures (proven reliability with cemented-on aluminium foil). |
| | | |
− | == Floating-drum plants ==
| |
| | | |
− | {| cellspacing="0" cellpadding="0" border="0" align="left" class="IMGleft"
| + | '''Disadvantages''' |
− | |-
| + | *Substantial consumption of essentially good-quality cement; |
− | |
| + | *workmanship must meet high quality standards; |
− | [[Image:Floating drum mauretania.jpg]]
| + | *uses substantial amounts of expensive wire mesh; |
| + | *construction technique not yet adequately time-tested; |
| + | *special sealing measures for the gas-holder are necessary. Ferro-cement biogas plants are only recommended in cases where special ferro-cement know-how is available. |
| | | |
− | <small class="IMGLEGEND">'''Floating-drum plant in Mauretania'''<br> </small><small class="IMGSOURCE">''Photo: gtz/GATE''</small> <br>
| |
| | | |
− | |} | + | [[#toc|►Go to Top]]<br/> |
| | | |
− | <br>
| + | = Industrial Digester Types = |
| | | |
− | === The drum === | + | {| class="IMGright FCK__ShowTableBorders" border="0" cellpadding="10" align="right" style="width: 378px;" |
− | | |
− | In the past, floating-drum plants were mainly built in India. A floating-drum plant consists of a cylindrical or dome-shaped digester and a moving, floating gas-holder, or drum. The gas-holder floats either directly in the fermenting slurry or in a separate water jacket. The drum in which the biogas collects has an internal and/or external guide frame that provides stability and keeps the drum upright. If biogas is produced, the drum moves up, if gas is consumed, the gas-holder sinks back. <br>
| |
− | | |
− | <br>
| |
− | | |
− | === Size ===
| |
− | | |
− | Floating-drum plants are used chiefly for digesting animal and human feces on a continuous-feed mode of operation, i.e. with daily input. They are used most frequently by small- to middle-sized farms (digester size: 5-15m<sup>3</sup>) or in institutions and larger agro-industrial estates (digester size: 20-100m<sup>3</sup>).
| |
− | <blockquote>'''''Advantages''''': Floating-drum plants are easy to understand and operate. They provide gas at a constant pressure, and the stored gas-volume is immediately recognizable by the position of the drum. Gas-tightness is no problem, provided the gasholder is de-rusted and painted regularly. </blockquote> <blockquote>
| |
− | '''''Disadvantages''''': The steel drum is relatively expensive and maintenance-intensive. Removing rust and painting has to be carried out regularly. The life-time of the drum is short (up to 15 years; in tropical coastal regions about five years). If fibrous substrates are used, the gas-holder shows a tendency to get "stuck" in the resultant floating scum.
| |
− | </blockquote>
| |
− | {| width="300" cellpadding="10" border="0" align="left" class="IMGleft"
| |
| |- | | |- |
− | | [[Image:Floatdrumschemewaterjack s.gif]]<small class="IMGLEGEND">'''Water-jacket plant with external guide frame. 1 Mixing pit, 11 Fill pipe, 2 Digester, 3 Gasholder, 31 Guide frame, 4 Slurry store, 5 Gas pipe'''<br> </small><small class="IMGSOURCE">''Source: Sasse, 1984''</small> <br> | + | | [[File:Indsolcontrol.jpg|378px|RTENOTITLE]]<small class="IMGLEGEND">Control glasses for an industrial digester for solid organic waste, Germany</small><ref name="TBW">TBW</ref><br/> |
| |} | | |} |
| | | |
− | <br>
| + | To give an overview, some fictitious designs have been chosen as they could be found in, for example, Europe. The designs are selected in a way that all the typical elements of modern biogas technology appear at least once. All designs are above-ground, which is common in Europe. Underground structures, however, do exist. |
| | | |
− | === Water-jacket floating-drum plants ===
| |
| | | |
− | Water-jacket plants are universally applicable and easy to maintain. The drum cannot get stuck in a scum layer, even if the substrate has a high solids content. Water-jacket plants are characterized by a long useful life and a more aesthetic appearance (no dirty gas-holder). Due to their superior sealing of the substrate (hygiene!), they are recommended for use in the fermentation of night soil. The extra cost of the masonry water jacket is relatively modest. <br> <br>
| + | '''Mixing pit''' varies in size and shape according to the nature of substrate. It is equipped with propellers for mixing and/or chopping the substrate and often with a pump to transport the substrate into the digester. At times, the substrate is also pre-heated in the mixing pit in order to avoid a temperature shock inside the digester. |
| | | |
− | === Material of digester and drum ===
| + | <br/> |
| | | |
− | The digester is usually made of brick, concrete or quarry-stone masonry with plaster. The gas drum normally consists of 2.5 mm steel sheets for the sides and 2 mm sheets for the top. It has welded-in braces which break up surface scum when the drum rotates. The drum must be protected against corrosion. Suitable coating products are oil paints, synthetic paints and bitumen paints. Correct priming is important. There must be at least two preliminary coats and one topcoat. Coatings of used oil are cheap. They must be renewed monthly. Plastic sheeting stuck to bitumen sealant has not given good results. In coastal regions, repainting is necessary at least once a year, and in dry uplands at least every other year. Gas production will be higher if the drum is painted black or red rather than blue or white, because the digester temperature is increased by solar radiation. Gas drums made of 2 cm wire-mesh-reinforced concrete or fiber-cement must receive a gas-tight internal coating. The gas drum should have a slightly sloping roof, otherwise rainwater will be trapped on it, leading to rust damage. An excessively steep-pitched roof is unnecessarily expensive and the gas in the tip cannot be used because when the drum is resting on the bottom, the gas is no longer under pressure.
| + | '''Fermenter or digester''' is insulated and made of concrete or steel. To optimize the flow of substrate, large digesters have a longish channel form. Large digesters are almost always agitated by slow rotating paddles or rotors or by injected biogas. Co-fermenters have two or more separated fermenters. The gas can be collected inside the digester, then usually with a flexible cover. The digester can also be filled completely and the gas stored in a separate gas-holder. |
| | | |
− | Floating-drums made of glass-fiber reinforced plastic and high-density polyethylene have been used successfully, but the construction costs are higher compared to using steel. Floating-drums made of wire-mesh-reinforced concrete are liable to hairline cracking and are intrinsically porous. They require a gas-tight, elastic internal coating. PVC drums are unsuitable because they are not resistant to UV.
| + | <br/> |
| | | |
− | <br>
| + | '''Gas-holder''' is usually of flexible material, therefore to be protected against weather. It can be placed either directly above the substrate, then it acts like a balloon plant, or in a separate 'gas-bag'. |
| | | |
− | === Guide frame ===
| + | <br/> |
| | | |
− | The side wall of the gas drum should be just as high as the wall above the support ledge. The floating-drum must not touch the outer walls. It must not tilt, otherwise the coating will be damaged or it will get stuck. For this reason, a floating-drum always requires a guide. This guide frame must be designed in a way that allows the gas drum to be removed for repair. The drum can only be removed if air can flow into it, either by opening the gas outlet or by emptying the water jacket.
| + | '''Slurry store''' for storage of slurry during winter. The store can be open (like conventional open liquid manure storage) or closed and connected to the gas-holder to capture remaining gas production. Normally, the store is not heated and only agitated before the slurry is spread on the field. |
| | | |
− | The floating gas drum can be replaced by a balloon above the digester. This reduces construction costs but in practice problems always arise with the attachment of the balloon to the digester and with the high susceptibility to physical damage.
| + | <br/> |
| | | |
− | <br>
| + | '''Gas use element''' is in Europe in 95% of the cases a thermo-power unit which produces electricity for the farm, the grid and heat for the house, greenhouses and other uses. The thermo-power unit has the advantage, that the required energy can be produced in any mixture of gas and fossil energy. It can, therefore, react to periods of low gas production and high energy requirements or vice versa. |
| | | |
− | === Types of floating-drum plants ===
| + | <br/> |
| | | |
− | There are different types of floating-drum plants:
| + | {| style="width: 500px;" class="IMGcenter FCK__ShowTableBorders" border="0" cellpadding="0" cellspacing="0" align="center" |
| + | |- |
| + | | <p style="text-align: center;">[[File:Concretedigest1.gif|550px|RTENOTITLE]]</p> |
| + | <small class="IMGLEGEND">'''Concrete digester with two chambers (one heated, one unheated for storage)'''</small><ref name="TBW">TBW</ref> |
| | | |
− | *'''KVIC model''' with a cylindrical digester, the oldest and most widespread floating drum biogas plant from India.
| + | |} |
− | *'''Pragati model''' with a hemisphere digester
| |
− | *'''Ganesh model''' made of angular steel and plastic foil
| |
− | *floating-drum plant made of pre-fabricated reinforced concrete compound units
| |
− | *floating-drum plant made of fibre-glass reinforced polyester
| |
− | *'''BORDA model: '''The BORDA-plant combines the static advantages of hemispherical digester with the process-stability of the floating-drum and the longer life span of a water jacket plant.
| |
| | | |
− | <br>
| + | {| style="width: 500px;" class="IMGcenter FCK__ShowTableBorders" border="0" cellpadding="0" cellspacing="0" align="center" |
| + | |- |
| + | | |
| + | [[File:Concretedigest2.gif|550px|RTENOTITLE]] |
| | | |
− | === Further reading: === | + | <small class="IMGLEGEND">'''Concrete digester with integrated plastic gas-holder'''</small><ref name="TBW">TBW</ref> |
| | | |
− | '''''English:'''''
| + | |} |
− | | |
− | *Amaratunga, M.: Structural Behaviour and Stress Conditions of Fixed Dome Type of Biogas Units. Elhalwagi, M.M. (Ed.): Biogas Technology, Transfer and Diffusion, London & New York, pp. 295-301. 1986. 0001182; ISBN: 1-85166-000-3
| |
− | *van Buren, A.; Crook, M.: A Chinese Biogas Manual - Popularising Technology in the Countryside. Intermediate Technology Publications Ltd. London (UK), 1979, sixth impression 1985, 135 P. ISBN: 0903031655
| |
− | *Fulford, D.: Fixed Concrete Dome Design. Biogas - Challenges and Experience from Nepal. Vol I. United Mission to Nepal, 1985, pp. 3.1-3.10.
| |
− | *Ringkamp, M. - FH Hildesheim/Holzminden/Faculty of Civil Engineering Holzminden (Germany): Regional Biogas Extension Programme GCR - Final Report on Statical and Structural Examination of Caribbean Biogas Plants. 1989, 60 P.
| |
− | *Sasse, L. - GATE, Bremer Arbeitsgemeinschaft für Überseeforschung und Entwicklung (BORDA): Biogas Plants - Design and Details of Simple Biogas Plants. 2nd edition, 1988, 85 P., ISBN: 3-528-02004-0
| |
− | *Werner, U., St�hr, U., Hees, N. - GATE: Biogas Plants in Animal Husbandry - A Practical Guide. Friedr. Vieweg & Sohn, Braunschweig/Wiesbaden (Germany), 1989; 153 p., ISBN: 3-528-02048-2
| |
− | | |
− | '''''''Espanol:'''''
| |
− | | |
− | *Sasse, L. - Centro de Investigacion, Estudios y Documentacion (CIED) Lima (Peru): La Planta de Biogas - Bosquejo y Detaille de Plantas Simples. Reciclaje de la Materia Organica 3. 1986. 103 p.
| |
− | | |
− | '''''Deutsch:'''''
| |
− | | |
− | *Sasse, L. - GATE; Bremer Arbeitsgemeinschaft für Überseeforschung und Entwicklung (BORDA): Die Biogas-Anlage - Entwurf und Detail einfacher Anlagen. 2. Aufl. 1987, 85 P., ISBN: 3-528-01003-2
| |
− | *Sasse, L.: Biogas in der GTZ - Zur Statik von Festdomanlagen. Biogas Information Nr. 27. 1988, pp. 19-24
| |
− | *Werner, U.; St�hr, U.; Hees, N.: Praktischer Leitfaden für Biogasanlagen in der Tierproduktion. Sonderpublikation der GTZ Nr. 180. 1986. ISBN: 3-88085-311-8
| |
− | | |
− | <br>
| |
| | | |
− | == Low-Cost Polyethylen Tube Digester ==
| + | {| style="width: 500px;" class="IMGcenter FCK__ShowTableBorders" border="0" cellpadding="0" cellspacing="0" align="center" |
− | | |
− | ==== Digester ====
| |
− | | |
− | ----
| |
− | | |
− | The Low-Cost Polyethylene Tube Digester consist in utilize the tubular polyethylene (in this case in black color) employed in his natural transparent color for greenhouses, to dispose a chamber of various cubic meters hermetical isolated. In the model which is used in Bolivia, the film of the tubular polyethylene (two coats of 300 microns) will bended at his both extremes each around a 6 inch pvc drainpipe and will wound with band of recycled car wheels. With this system, calculated adequately the inclination of the indicated pipes, one obtains a hermetic tank (figure td1).<br>
| |
− | | |
− | {| cellpadding="10" border="0" align="right" style="width: 547px; height: 282px;" | |
| |- | | |- |
| | | | | |
− | [[Image:Low Cost Polyethylene Tube Digester Scheme.jpg|right]] | + | [[File:Concretedigest3.gif|550px|RTENOTITLE]] |
− | | |
− | <br>
| |
| | | |
− | <br> | + | <br/> |
| | | |
− | Figure td1: Scheme of Low-Cost Polyethylene Tube Digester<br>'''''<span lang="EN-US" style="font-size: 10pt; line-height: 115%;">Source: GTZ / EnDev Bolivia</span>''''' <br>
| + | '''<small class="IMGLEGEND"><span data-scaytid="7" data-scayt_word="Steelvessel">Steelvessel</span> fermenter with <span data-scaytid="8" data-scayt_word="seperate">seperate</span> <span data-scaytid="9" data-scayt_word="ballon">ballon</span> gas-holder</small><ref name="TBW">TBW</ref>''' |
| | | |
| |} | | |} |
| | | |
− | Because the tubular polyethylene is flexible, it is necesary to construct a "cradle" which will accommodate the reaction tank, so that one will dig a trench or build two parallel walls. One of the 6" pvc drainpipes serve as inlet and the other one as the outlet of the slurry.<br>
| + | <br/> |
− | | |
− | In the tube digester finally a hidraulic level will set up by itself, so that as much quantity of added prime matter (the mix of dung and water) as quantity of fertilizer leave by the outlet.<br>
| |
− | | |
− | ==== Gasholder and Gas Storage Reservoir ====
| |
− | | |
− | ----
| |
− | | |
− | The capacity of the gasholder corresponds to 1/3 of the total capacity of the reaction tube (figure td1). To overcome the problem of low rates of gas flow, one installed close proximity to the kitchen, a 150 micron tubular polyethylene reservoir, which gives a 2-3 m³ additional gas storage.<br>
| |
− | | |
− | ==== <span class="mw-headline">Biogas Supply Line</span> ====
| |
− | | |
− | ----
| |
− | | |
− | The track of biogas up to the kitchen one realise directly, keeping up the whole digester system with a maximal pressure of around 20 cm water column. This pressure one controlled with an in the line integrated security valve, which is constructed of a refreshment bottle.
| |
− | | |
− | <br>
| |
− | | |
− | <br>
| |
− | | |
− | <br>
| |
− | | |
− | <br>
| |
− | | |
− | <br>
| |
− | | |
− | <br>
| |
− | | |
− | <br>
| |
− | | |
− | <br>
| |
− | | |
− | <br>
| |
− | | |
− | <br>
| |
− | | |
− | <br>
| |
− | | |
− | = Biogas Plant Types and Design =
| |
| | | |
− | == Digester types in industrialized countries ==
| + | [[#toc|►Go to Top]] |
| | | |
− | {| width="378" cellpadding="10" border="0" align="right" class="IMGright"
| + | == Batch plants == |
− | |-
| |
− | | [[Image:Indsolcontrol.jpg]]<small class="IMGLEGEND">'''Control glasses for an industrial digester for solid organic waste, TBW, Germany'''<br> </small><br>
| |
− | |}
| |
| | | |
− | To give an overview, we have chosen three fictitious designs as they could be found in, for example, Europe. The designs are selected in a way that all the typical elements of modern biogas technology appear at least once. All designs are above-ground, which is common in Europe. Underground structures, however, do exist.
| + | Batch plants are filled and then emptied completely after a fixed retention time. Each design and each fermentation material is suitable for batch filling, but batch plants require high labor input. As a major disadvantage, their gas-output is not steady. |
| | | |
− | '''Mixing pit '''varies in size and shape according to the nature of substrate. It is equipped with propellers for mixing and/or chopping the substrate and often with a pump to transport the substrate into the digester. At times, the substrate is also pre-heated in the mixing pit in order to avoid a temperature shock inside the digester.
| + | [[#toc|►Go to Top]] |
| | | |
− | '''Fermenter or digester '''is insulated and made of concrete or steel. To optimize the flow of substrate, large digesters have a longish channel form. Large digesters are almost always agitated by slow rotating paddles or rotors or by injected biogas. Co-fermenters have two or more separated fermenters. The gas can be collected inside the digester, then usually with a flexible cover. The digester can also be filled completely and the gas stored in a separate gas-holder.
| + | === Continuous plants<br/> === |
| | | |
− | '''Gas-holder''' is usually of flexible material, therefore to be protected against weather. It can be placed either directly above the substrate, then it acts like a balloon plant, or in a separate 'gas-bag'.
| + | Continuous plants are fed and emptied continuously. They empty automatically through the overflow whenever new material is filled in. Therefore, the substrate must be fluid and homogeneous. Continuous plants are suitable for rural households as the necessary work fits well into the daily routine. Gas production is constant, and higher than in batch plants. Today, nearly all biogas plants are operating on a continuous mode. |
| | | |
− | '''slurry store''' for storage of slurry during winter. The store can be open (like conventional open liquid manure storage) or closed and connected to the gas-holder to capture remaining gas production. Normally, the store is not heated and only agitated before the slurry is spread on the field.
| + | [[#toc|►Go to Top]] |
| | | |
− | '''Gas use element''' is in Europe in 95% of the cases a thermo-power unit which produces electricity for the farm, the grid and heat for the house, greenhouses and other uses. The thermo-power unit has the advantage, that the required energy can be produced in any mixture of gas and fossil energy. It can, therefore, react to periods of low gas production and high energy requirements or vice versa.
| + | === Semi-batch basis<br/> === |
| | | |
− | {| cellspacing="0" cellpadding="0" border="0" class="IMGcenter"
| + | If straw and dung are to be digested together, a biogas plant can be operated on a semi-batch basis. The slowly digested straw-type material is fed in about twice a year as a batch load. The dung is added and removed regularly. |
− | |-
| |
− | | width="45%" | <br>
| |
− | | [[Image:Concretedigest1.gif]]<small class="IMGLEGEND">'''Concrete digester with two chambers (one heated, one unheated for storage)'''<br> </small><small class="IMGSOURCE">''Source: TBW''</small>
| |
− | | width="45%" | <br>
| |
− | |}
| |
| | | |
− | {| cellspacing="0" cellpadding="0" border="0" class="IMGcenter"
| + | [[#toc|►Go to Top]] |
− | |-
| |
− | | width="45%" | <br>
| |
− | | [[Image:Concretedigest2.gif]]<small class="IMGLEGEND">'''Concrete digester with integrated plastic gas-holder'''<br> </small><small class="IMGSOURCE">''Photo: TBW''</small>
| |
− | | width="45%" | <br>
| |
− | |}
| |
| | | |
− | {| cellspacing="0" cellpadding="0" border="0" class="IMGcenter"
| |
− | |-
| |
− | | width="45%" | <br>
| |
− | | [[Image:Concretedigest3.gif]]<small class="IMGLEGEND">'''Steelvessel fermenter with seperate ballon gas-holder'''<br> </small><small class="IMGSOURCE">''Photo: TBW''</small>
| |
− | | width="45%" | <br>
| |
− | |}
| |
| | | |
− | == Selection of appropriate design == | + | = Dry Fermentation Plants<br/> = |
| | | |
− | In developing countries, the design selection is determined largely be the prevailing design in the region, which, in turn takes the climatic, economic and substrate specific conditions into consideration. Large plants are designed on a case-to-case basis.
| + | Dry fermentation is an anaerobic process in which micro-organism break down biodegradable material. Renewable organic feedstocks are used as a the source of energy for the process. The nutrient-rich solids resulting from the digestion can be used as a fertiliser subsequently. |
| | | |
− | Typical design criteria are:
| + | Almost any organic material can be processed with dry fermentation. This includes biodegradable waste materials such as waste paper, grass clippings, leftover food, sewage and animal waste. |
| | | |
− | '''Space''': determines mainly the decision if the fermenter is above-ground or underground, if it is to be constructed as an upright cylinder or as a horizontal plant.
| + | <br/> |
| | | |
− | '''Existing structures''' may be used like a liquid manure tank, an empty hall or a steel container. To reduce costs, the planner may need to adjust the design to theses existing structures. | + | <u>'''Process'''</u><br/> |
| + | *[[:file:VTI_Dry_fermentation_biogas_in_Germany.pdf|Dry fermentation in germany]] (vTI presentation, 2 MB) |
| | | |
− | '''Minimizing costs''' can be an important design parameter, especially when the monetary benefits are expected to be low. In this case a flexible cover of the digester is usually the cheapest solution. Minimizing costs is often opposed to maximizing gas yield.
| + | <br/> |
| | | |
− | '''Available substrate''' determines not only the size and shape of mixing pit but the digester volume (retention time!), the heating and agitation devices. Agitation through gas injection is only feasible with homogenous substrate and a dry matter content below 5%. Mechanical agitation becomes problematic above 10% dry matter.
| + | [[Types_of_Biogas_Digesters_and_Plants#toc|►Go to Top]] |
| | | |
− | == Ballon plants ==
| + | <br/> |
| | | |
− | A balloon plant consists of a heat-sealed plastic or rubber bag (balloon), combining digester and gas-holder. The gas is stored in the upper part of the balloon. The inlet and outlet are attached directly to the skin of the balloon. Gas pressure can be increased by placing weights on the balloon. If the gas pressure exceeds a limit that the balloon can withstand, it may damage the skin. Therefore, safety valves are required. If higher gas pressures are needed, a gas pump is required. Since the material has to be weather- and UV resistant, specially stabilized, reinforced plastic or synthetic caoutchouc is given preference. Other materials which have been used successfully include RMP (red mud plastic), Trevira and butyl. The useful life-span does usually not exceed 2-5 years.
| + | = Further Information<br/> = |
| + | <u>'''English'''</u><br/> |
| + | *Amaratunga, M.: Structural Behaviour and Stress Conditions of Fixed Dome Type of Biogas Units. Elhalwagi, M.M. (Ed.): Biogas Technology, Transfer and Diffusion, London & New York, pp. 295-301. 1986. 0001182; ISBN: 1-85166-000-3 |
| + | *van Buren, A.; Crook, M.: A Chinese Biogas Manual – Popularizing Technology in the Countryside. Intermediate Technology Publications Ltd. London (UK), 1979, sixth impression 1985, 135 P. ISBN: 0903031655 |
| + | *Fulford, D.: Fixed Concrete Dome Design. Biogas - Challenges and Experience from Nepal. Vol I. United Mission to Nepal, 1985, pp.3.1-3.10. |
| + | *Ringkamp , M. – FH Hildesheim Holzminden/Faculty of Civil Engineering Holzminden (Germany): Regional Biogas Extension Programme GCR - Final Report on Statistical and Structural Examination of Caribbean Biogas Plants. 1989, 60 P. |
| + | *Sasse, L. - GATE, Bremer Arbeitsgemeinschaft für Überseeforschung Entwicklung (BORDA): Biogas Plants - Design and Details of Simple Biogas Plants. 2nd edition, 1988, 85 P., ISBN: 3-528-02004-0 |
| + | *Werner, U., Stoh, U., Hees, N. - GATE: Biogas Plants in Animal Husbandry - A Practical Guide. Friedr. Vieweg & Sohn, Braunschweig/Wiesbaden (Germany), 1989; 153 p., ISBN: 3-528-02048-2 |
| + | * Sasse, L. - Centro de Investigacion, Estudios y Documentacion (CIED) Lima (Peru): La Planta de Biogas - Bosquejo y Detaille de Plantas Simples. Reciclaje de la Materia Organica 3. 1986. 103 p. |
| | | |
− | '''''Advantages''''': Standardized prefabrication at low cost; shallow installation suitable for use in areas with a high groundwater table; high digester temperatures in warm climates; uncomplicated cleaning, emptying and maintenance; difficult substrates like water hyacinths can be used. </div> '''''Disadvantages''''': Low gas pressure may require gas pumps; scum cannot be removed during operation; the plastic balloon has a relatively short useful life-span and is susceptible to mechanical damage and usually not available locally. In addition, local craftsmen are rarely in a position to repair a damaged balloon. </div> Balloon biogas plants are recommended, if local repair is or can be made possible and the cost advantage is substantial.
| + | <br/> |
| | | |
− | == Horizontal plants ==
| + | <u>Articles on energypedia</u> |
| + | *[http://www.biogaspartner.de/en/biowhat-biomethane/value-chain/biogas-upgrade.html How to upgrade biogas on BIOGASPARTNER] |
| + | *[http://www1.agric.gov.ab.ca/$department/deptdocs.nsf/all/bdv11206/$file/biogasplantdatasheets0606.pdf?OpenElement Data sheets of biogas plants] |
| + | *[[Plastic Tube Digesters in Kenya|Plastic tube digester (domestic).]] |
| + | *[[Low-Cost Polyethylene Tube Digesters in Bolivia|Polyethylene digester in Bolivia.]] |
| + | *[[Biogas Technology in India|Biogas technology in India.]] |
| + | *[https://energypedia.info/index.php/Types_of_Biogas_Digesters_and_Plants Types of biogas digesters and plants (mainly domestic applications)] |
| | | |
− | Horizontal biogas plants are usually chosen when shallow installation is called for (groundwater, rock). They are made of masonry or concrete.
| |
− | <blockquote>'''''Advantages''''': Shallow construction despite large slurry space. </blockquote> <blockquote>
| |
− | '''''Disadvantages''''': Problems with gas-space leakage, difficult elimination of scum.
| |
− | </blockquote>
| |
− | == Earth-pit plants ==
| |
| | | |
− | Masonry digesters are not necessary in stable soil (e.g. laterite). It is sufficient to line the pit with a thin layer of cement (wire-mesh fixed to the pit wall and plastered) in order to prevent seepage. The edge of the pit is reinforced with a ring of masonry that also serves as anchorage for the gas-holder. The gas-holder can be made of metal or plastic sheeting. If plastic sheeting is used, it must be attached to a quadratic wooden frame that extends down into the slurry and is anchored in place to counter its buoyancy. The requisite gas pressure is achieved by placing weights on the gas-holder. An overflow point in the peripheral wall serves as the slurry outlet.
| + | [[#toc|►Go to Top]] |
− | <blockquote>'''''Advantages''''': Low cost of installation (as little as 20% of a floating-drum plant); high potential for self help approaches. </blockquote> <blockquote>
| |
− | '''''Disadvantages''''': Short useful life; serviceable only in suitable, impermeable types of soil.
| |
− | </blockquote>
| |
− | Earth-pit plants can only be recommended for installation in impermeable soil located above the groundwater table. Their construction is particularly inexpensive in connection with plastic sheet gas-holders.
| |
| | | |
− | == Ferrocement plants ==
| |
| | | |
− | The ferro-cement type of construction can be applied either as a self-supporting shell or an earth-pit lining. The vessel is usually cylindrical. Very small plants (Volume under 6 m<sup>3</sup>) can be prefabricated. As in the case of a fixed-dome plant, the ferrocement gasholder requires special sealing measures (proven reliability with cemented-on aluminium foil).
| + | = References<br/> = |
− | <blockquote>'''''Advantages''''': Low cost of construction, especially in comparison with potentially high cost of masonry for alternative plants; mass production possible; low material input. </blockquote> <blockquote>
| |
− | '''''Disadvantages''''': Substantial consumption of essentially good-quality cement; workmanship must meet high quality standards; uses substantial amounts of expensive wire mesh; construction technique not yet adequately time-tested; special sealing measures for the gas-holder are necessary.
| |
− | </blockquote> | |
− | Ferro-cement biogas plants are only recommended in cases where special ferro-cement know-how is available. <!-- Navigation Footer --> <br>
| |
| | | |
− | <br>
| + | This article is based on the following publication: |
| | | |
− | <br> <br>
| + | GTZ: [[:File:Biogas gate volume 2.pdf|Biogas Digest Volume II: Biogas - Application and Product Development]] |
| | | |
− | [[Biogas|back to "Biogas" section]]
| + | <references /> |
− | <br></div></div>
| |
| | | |
| + | [[Category:Bioenergy]] |
| [[Category:Biogas]] | | [[Category:Biogas]] |
►Back to Biogas Portal
Introduction
Construction of the digester neck with steel reinforcement[1]
|
Choosing a right biogas digester is a very important while constructing a biogas plant. From the standpoint of fluid dynamics and structural strength, an egg-shaped vessel is about the best possible solution. This type of construction, however, is comparatively expensive, therefore, its use is usually restricted to large-scale sewage treatment plants. The Chinese fixed-dome designs are of similar shape, but less expensive. The hemispherical CAMARTEC design is optimized in structural strength, but does not make optimal use of the excavation required.
Simplified versions of such digester designs include cylinders with conical covers and bottoms. They are much easier to build and are sometimes available on the market as prefabricated units. Their disadvantage lies in their less favorable surface-volume ratio. The cylinder should have a height equal to its diameter. Prone cylinders have become quite popular on farms, since they are frequently the more favorable solution for small-scale bio-methanation. Cuboid digesters are often employed in batch-fed systems used primarily for fermenting solid material, so that fluid dynamics are of little interest.
Types of Small-Scale Digesters
Fixed Dome Biogas Plants
A fixed-dome plant comprises of a closed, dome-shaped digester with an immovable, rigid gas-holder and a displacement pit, also named 'compensation tank'. The gas is stored in the upper part of the digester. When gas production commences, the slurry is displaced into the compensating tank. Gas pressure increases with the volume of gas stored, i.e. with the height difference between the two slurry levels. If there is little gas in the gas-holder, the gas pressure is low.
►Read more here...
Floating Drum Plants
Floating-drum plants consist of an underground digester and a moving gas-holder. The gas-holder floats either directly on the fermentation slurry or in a water jacket of its own. The gas is collected in the gas drum, which rises or moves down, according to the amount of gas stored.
►Read more here...
Low-Cost Polyethylene Tube Digester
The Low-Cost Polyethylene Tube Digester model consist of tubular polyethylene film (two coats of 300 microns) bent at each end around a 6 inch PVC drainpipe and is wound with rubber strap of recycled tire-tubes.
►Read more here....
Balloon Plants
A balloon plant consists of a heat-sealed plastic or rubber bag (balloon), combining digester and gas-holder. The gas is stored in the upper part of the balloon. The inlet and outlet are attached directly to the skin of the balloon.
►Read more here...
Horizontal Plants
Disadvantages: Problems with gas-space leakage, difficult elimination of scum.
►Go to Top
Earth-pit Plants
Masonry digesters are not necessary in stable soil (e.g. laterite). It is sufficient to line the pit with a thin layer of cement (wire-mesh fixed to the pit wall and plastered) in order to prevent seepage. The edge of the pit is reinforced with a ring of masonry that also serves as anchorage for the gas-holder. The gas-holder can be made of metal or plastic sheeting. If plastic sheeting is used, it must be attached to a quadratic wooden frame that extends down into the slurry and is anchored in place to counter its buoyancy. The requisite gas pressure is achieved by placing weights on the gas-holder. An overflow point in the peripheral wall serves as the slurry outlet.
Advantages
- Low cost of installation (as little as 20% of a floating-drum plant);
- high potential for self help approaches.
Disadvantages
- Short useful life; serviceable only in suitable, impermeable types of soil.
- Earth-pit plants can only be recommended for installation in impermeable soil located above the groundwater table. Their construction is particularly inexpensive in connection with plastic sheet gas-holders.
►Go to Top
Ferro-cement Plants
The ferro-cement type of construction can be applied either as a self-supporting shell or an earth-pit lining. The vessel is usually cylindrical. Very small plants (Volume under 6 m3) can be prefabricated. As in the case of a fixed-dome plant, the ferrocement gasholder requires special sealing measures (proven reliability with cemented-on aluminium foil).
Disadvantages
- Substantial consumption of essentially good-quality cement;
- workmanship must meet high quality standards;
- uses substantial amounts of expensive wire mesh;
- construction technique not yet adequately time-tested;
- special sealing measures for the gas-holder are necessary. Ferro-cement biogas plants are only recommended in cases where special ferro-cement know-how is available.
►Go to Top
Industrial Digester Types
Control glasses for an industrial digester for solid organic waste, Germany[2]
|
To give an overview, some fictitious designs have been chosen as they could be found in, for example, Europe. The designs are selected in a way that all the typical elements of modern biogas technology appear at least once. All designs are above-ground, which is common in Europe. Underground structures, however, do exist.
Mixing pit varies in size and shape according to the nature of substrate. It is equipped with propellers for mixing and/or chopping the substrate and often with a pump to transport the substrate into the digester. At times, the substrate is also pre-heated in the mixing pit in order to avoid a temperature shock inside the digester.
Fermenter or digester is insulated and made of concrete or steel. To optimize the flow of substrate, large digesters have a longish channel form. Large digesters are almost always agitated by slow rotating paddles or rotors or by injected biogas. Co-fermenters have two or more separated fermenters. The gas can be collected inside the digester, then usually with a flexible cover. The digester can also be filled completely and the gas stored in a separate gas-holder.
Gas-holder is usually of flexible material, therefore to be protected against weather. It can be placed either directly above the substrate, then it acts like a balloon plant, or in a separate 'gas-bag'.
Slurry store for storage of slurry during winter. The store can be open (like conventional open liquid manure storage) or closed and connected to the gas-holder to capture remaining gas production. Normally, the store is not heated and only agitated before the slurry is spread on the field.
Gas use element is in Europe in 95% of the cases a thermo-power unit which produces electricity for the farm, the grid and heat for the house, greenhouses and other uses. The thermo-power unit has the advantage, that the required energy can be produced in any mixture of gas and fossil energy. It can, therefore, react to periods of low gas production and high energy requirements or vice versa.
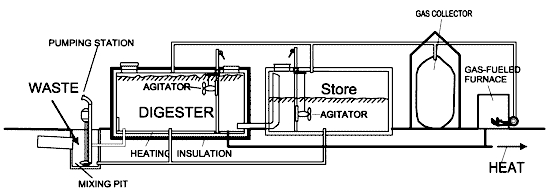
Concrete digester with two chambers (one heated, one unheated for storage)[2]
|
Concrete digester with integrated plastic gas-holder[2]
|
Steelvessel fermenter with seperate ballon gas-holder[2]
|
►Go to Top
Batch plants
Batch plants are filled and then emptied completely after a fixed retention time. Each design and each fermentation material is suitable for batch filling, but batch plants require high labor input. As a major disadvantage, their gas-output is not steady.
►Go to Top
Continuous plants
Continuous plants are fed and emptied continuously. They empty automatically through the overflow whenever new material is filled in. Therefore, the substrate must be fluid and homogeneous. Continuous plants are suitable for rural households as the necessary work fits well into the daily routine. Gas production is constant, and higher than in batch plants. Today, nearly all biogas plants are operating on a continuous mode.
►Go to Top
Semi-batch basis
If straw and dung are to be digested together, a biogas plant can be operated on a semi-batch basis. The slowly digested straw-type material is fed in about twice a year as a batch load. The dung is added and removed regularly.
►Go to Top
Dry Fermentation Plants
Dry fermentation is an anaerobic process in which micro-organism break down biodegradable material. Renewable organic feedstocks are used as a the source of energy for the process. The nutrient-rich solids resulting from the digestion can be used as a fertiliser subsequently.
Almost any organic material can be processed with dry fermentation. This includes biodegradable waste materials such as waste paper, grass clippings, leftover food, sewage and animal waste.
Process
►Go to Top
Further Information
English
- Amaratunga, M.: Structural Behaviour and Stress Conditions of Fixed Dome Type of Biogas Units. Elhalwagi, M.M. (Ed.): Biogas Technology, Transfer and Diffusion, London & New York, pp. 295-301. 1986. 0001182; ISBN: 1-85166-000-3
- van Buren, A.; Crook, M.: A Chinese Biogas Manual – Popularizing Technology in the Countryside. Intermediate Technology Publications Ltd. London (UK), 1979, sixth impression 1985, 135 P. ISBN: 0903031655
- Fulford, D.: Fixed Concrete Dome Design. Biogas - Challenges and Experience from Nepal. Vol I. United Mission to Nepal, 1985, pp.3.1-3.10.
- Ringkamp , M. – FH Hildesheim Holzminden/Faculty of Civil Engineering Holzminden (Germany): Regional Biogas Extension Programme GCR - Final Report on Statistical and Structural Examination of Caribbean Biogas Plants. 1989, 60 P.
- Sasse, L. - GATE, Bremer Arbeitsgemeinschaft für Überseeforschung Entwicklung (BORDA): Biogas Plants - Design and Details of Simple Biogas Plants. 2nd edition, 1988, 85 P., ISBN: 3-528-02004-0
- Werner, U., Stoh, U., Hees, N. - GATE: Biogas Plants in Animal Husbandry - A Practical Guide. Friedr. Vieweg & Sohn, Braunschweig/Wiesbaden (Germany), 1989; 153 p., ISBN: 3-528-02048-2
- Sasse, L. - Centro de Investigacion, Estudios y Documentacion (CIED) Lima (Peru): La Planta de Biogas - Bosquejo y Detaille de Plantas Simples. Reciclaje de la Materia Organica 3. 1986. 103 p.
Articles on energypedia
►Go to Top
References
This article is based on the following publication:
GTZ: Biogas Digest Volume II: Biogas - Application and Product Development