Difference between revisions of "SPIS Toolbox - Water Pump"
***** (***** | *****) m (→Water pump) |
***** (***** | *****) m |
||
(64 intermediate revisions by 4 users not shown) | |||
Line 1: | Line 1: | ||
− | + | {{Get Informed}} | |
− | = Water | + | {| cellpadding="1" |
+ | |- | ||
+ | | {{Back to SPIS Toolbox 2}} | ||
+ | | | ||
+ | | {{Back to Get Informed}} | ||
+ | | | ||
+ | | {{Next Chapter}}[[SPIS_Toolbox_-_Monitoring_System|►Go to the Next Chapter]]</span></span></span> | ||
+ | |} | ||
+ | |||
+ | === '''<span style="color:#879637;">5. Water Pump</span>''' === | ||
− | Depending on the water source, there are two different possibilities for pump installation – submersible or surface. Surface pumps are often installed next to the water source | + | Depending on the water source, there are two different possibilities for pump installation – submersible or surface. Surface pumps are often installed next to the water source and suck water up on one side before “pushing” it away on the other side of the pump. Surface pumps can pump water up from a maximum depth of six meters. Submersible pumps are installed under water in wells and boreholes and “push up” the water. |
− | Submersible pumps are installed at depths ranging from 10 to 120 meters. Using control switches (such as float switches in water tanks and wells), submersible pumps can be operated in automatic mode. In contrast, surface mounted pumps usually require the attendance of an operator who regularly checks the surface pump’s priming behavior. Use of primary chambers and non-return valves can prevent loss of prime | + | Submersible pumps are installed at depths ranging from 10 to 120 meters. Using control switches (such as float switches in water tanks and wells), submersible pumps can be operated in automatic mode. In contrast, surface mounted pumps usually require the attendance of an operator who regularly checks the surface pump’s priming behavior. Use of primary chambers and non-return valves can prevent loss of prime. |
− | + | Surface pumps have several advantages if compared to submersible ones: they are cheaper, can be easier installed and accessed for maintenance and can be used for an easy/simple fertigation at the suction/intake side. | |
+ | Solar water pumps are generally constructed from non-corrosive stainless steel and are designed to pump clean water without any solids and fibers. The lifetime of a submersible motor pump strongly depends on the water and installation quality. If the pump is installed in a drilled well with a proper well casing (and thus reduced sediment intrusion), submersible pumps may reach lifetimes between 7–10 years. In very poorly constructed wells and boreholes with high sediment content, the hydraulic part of the water pump may have to be replaced after 2–3 years. In order to secure a safe system operation, two safety means are necessary: | ||
*a water level sensor installed in the storage tank that switches off the pump in order to avoid overflow; | *a water level sensor installed in the storage tank that switches off the pump in order to avoid overflow; | ||
+ | *a second water level sensor installed towards the base of the well to avoid dry running of the pump. | ||
+ | |||
+ | There are two types of pumps to be typically found in today’s solar pumping systems: centrifugal and helical rotor pumps. | ||
− | + | ===== '''Centrifugal pump''' ===== | |
+ | {| style="width:100%;" | ||
+ | |- | ||
+ | | | ||
+ | A centrifugal pump creates an increase in pressure by transferring mechanical energy from the motor to the fluid through the rotating impeller. The fluid flows through the inlet to the impeller center and out along its blades. The centrifugal force increases the fluid velocity and consequently the kinetic energy is transformed to pressure. The pressure can be increased by simply adding several stages in series. Centrifugal pumps are generally utilized where pumping heads are low and water demand is high. For this reason centrifugal pumps are the preferred option for use in irrigation systems. | ||
− | + | | [[File:Centrifugal Pump.png|thumb|right|100px|Centrifugal pump (Source: Grundfos)]] | |
+ | |} | ||
− | + | {{#widget:YouTube|id=hcnMGDLtb9U|height=300|width=800}} | |
− | + | ===== '''Helical Rotor Pump''' ===== | |
+ | {|style="width:100%;" | ||
|- | |- | ||
− | | | + | | A helical rotor pump is a type of progressive cavity pump that works by the rotation of a helical rotor when sealed against a helix wall, pushing discrete sections of material through the device. |
− | |||
− | + | This corkscrew-like action provides a pulse-free flow, and valves are not required as the helical rotor seals the discrete sections of material. The flow rate is determined by the rotor speed and is independent of outlet pressure. Helical rotor pumps are typically found in applications with high pumping heads and low water flow rates, such as for drinking water supply. | |
+ | | [[File:SurfPump.jpg|thumb|right|120px|Surface pump on a mobile structure (Source: Lennart Woltering)]] | ||
+ | |} | ||
− | | | + | {{#widget:YouTube|id=g2U88sQdp40|height=300|width=800}} |
− | |} | ||
− | + | ===== '''Positive Displacement Pump''' ===== | |
− | + | Positive displacement pumps are among the oldest pump technologies in the world. They can be installed under water (submersed) or above water as a «dry running machine». The pumps can be driven by wind, solar, animals, humans, or electricity from the grid. In some cases, you may need a gearbox to lower or increase the pump speed. | |
− | + | {{#widget:YouTube|id=HFJ7BB74JZc|height=300|width=800}} | |
− | + | {| cellpadding="1" | |
+ | |- | ||
+ | | {{Back to SPIS Toolbox 2}} | ||
+ | | | ||
+ | | {{Back to Get Informed}} | ||
+ | | | ||
+ | | {{Next Chapter}}[[SPIS_Toolbox_-_Monitoring_System|►Go to the Next Chapter]]</span></span></span> | ||
+ | |} | ||
+ | {{SPIS Reference}} |
Latest revision as of 19:25, 21 July 2020
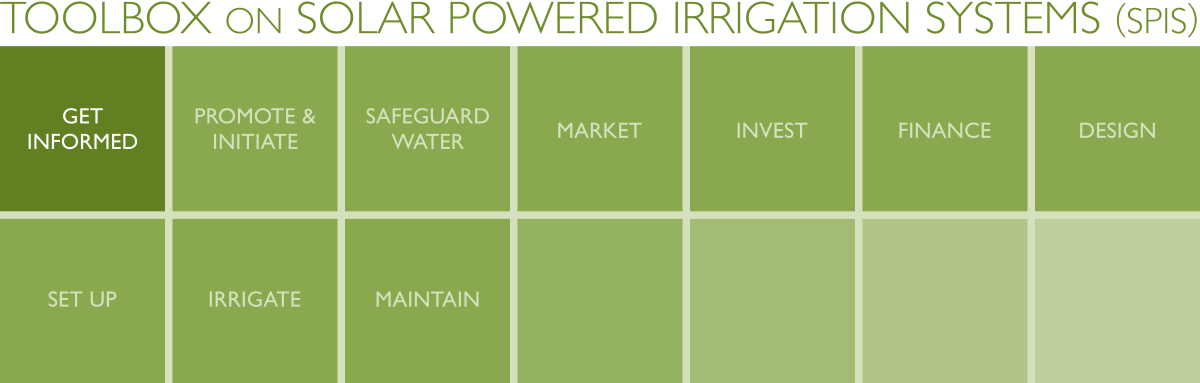
►Back to the Start Page | ►Back to the Module Page | ►Go to the Next Chapter |
5. Water Pump
Depending on the water source, there are two different possibilities for pump installation – submersible or surface. Surface pumps are often installed next to the water source and suck water up on one side before “pushing” it away on the other side of the pump. Surface pumps can pump water up from a maximum depth of six meters. Submersible pumps are installed under water in wells and boreholes and “push up” the water.
Submersible pumps are installed at depths ranging from 10 to 120 meters. Using control switches (such as float switches in water tanks and wells), submersible pumps can be operated in automatic mode. In contrast, surface mounted pumps usually require the attendance of an operator who regularly checks the surface pump’s priming behavior. Use of primary chambers and non-return valves can prevent loss of prime.
Surface pumps have several advantages if compared to submersible ones: they are cheaper, can be easier installed and accessed for maintenance and can be used for an easy/simple fertigation at the suction/intake side.
Solar water pumps are generally constructed from non-corrosive stainless steel and are designed to pump clean water without any solids and fibers. The lifetime of a submersible motor pump strongly depends on the water and installation quality. If the pump is installed in a drilled well with a proper well casing (and thus reduced sediment intrusion), submersible pumps may reach lifetimes between 7–10 years. In very poorly constructed wells and boreholes with high sediment content, the hydraulic part of the water pump may have to be replaced after 2–3 years. In order to secure a safe system operation, two safety means are necessary:
- a water level sensor installed in the storage tank that switches off the pump in order to avoid overflow;
- a second water level sensor installed towards the base of the well to avoid dry running of the pump.
There are two types of pumps to be typically found in today’s solar pumping systems: centrifugal and helical rotor pumps.
Centrifugal pump
A centrifugal pump creates an increase in pressure by transferring mechanical energy from the motor to the fluid through the rotating impeller. The fluid flows through the inlet to the impeller center and out along its blades. The centrifugal force increases the fluid velocity and consequently the kinetic energy is transformed to pressure. The pressure can be increased by simply adding several stages in series. Centrifugal pumps are generally utilized where pumping heads are low and water demand is high. For this reason centrifugal pumps are the preferred option for use in irrigation systems. |
Helical Rotor Pump
A helical rotor pump is a type of progressive cavity pump that works by the rotation of a helical rotor when sealed against a helix wall, pushing discrete sections of material through the device.
This corkscrew-like action provides a pulse-free flow, and valves are not required as the helical rotor seals the discrete sections of material. The flow rate is determined by the rotor speed and is independent of outlet pressure. Helical rotor pumps are typically found in applications with high pumping heads and low water flow rates, such as for drinking water supply. |
Positive Displacement Pump
Positive displacement pumps are among the oldest pump technologies in the world. They can be installed under water (submersed) or above water as a «dry running machine». The pumps can be driven by wind, solar, animals, humans, or electricity from the grid. In some cases, you may need a gearbox to lower or increase the pump speed.
►Back to the Start Page | ►Back to the Module Page | ►Go to the Next Chapter |