SPIS Toolbox - Controller and Inverter
Introduction
The Toolbox on Solar Powered Irrigation Systems (SPIS) is designed to enable advisors, service providers and practitioners in the field of solar irrigation to provide broad hands-on guidance to end-users, policy-makers and financiers. Risks related to system efficiency, financial viability and the unsustainable use of water resources can thus be minimized. The Toolbox comprises informative modules supplemented with user-friendly software tools (calculations sheets, checklists, guidelines). read more
Modules and tools touch upon:
- assessing the water requirements,
- comparing the financial viability,
- determining farm profitability and payback of investment in SPIS,
- sustainably design and maintain a SPIS,
- highlight critical workmanship quality aspects,
- and many more.
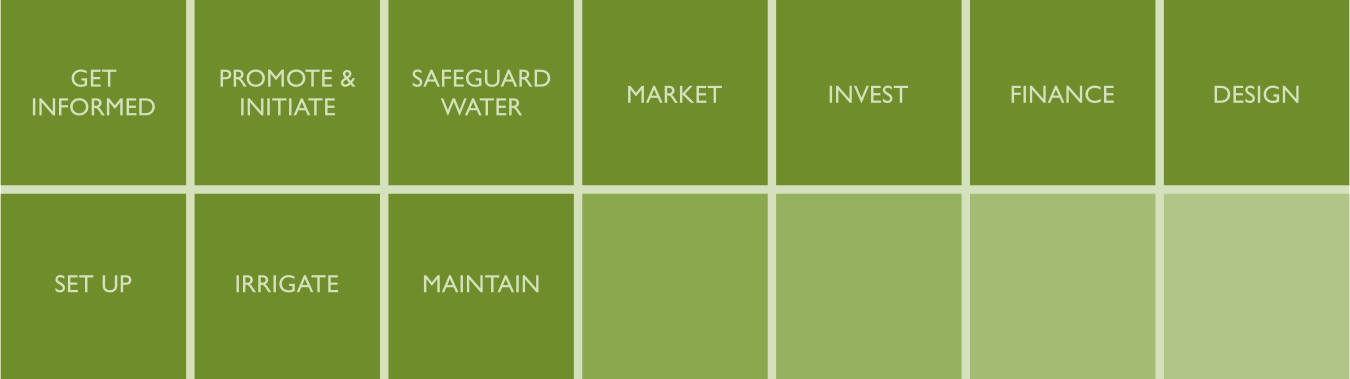
Controller and Inverter
Controller
The controller is the link between the solar generator and the motor pump and is essential for system reliability. It adjusts the fluctuation in the output frequency of the solar generator resulting from varying irradiation levels. Modern controllers incorporate highly efficient power electronics and utilize Maximum Power Point Tracking (MPPT) technology to maximize power use from the solar generator. The controller regulates the number of revolutions of the motor and protects the pump against over and under voltage, reverse polarity, overload and over-temperature.
Inverter
Solar generators always provide DC current. Most electric motors of solar water pumps are powered by direct current (DC). Since DC motors usually have a higher efficiency than AC motors of a similar size, they tend to be preferred by solar pump manufacturers. Water-filled brushless DC motors in particular are gaining importance because they are maintenance-free and are not affected by frequent starts/stops that are typical of solar-powered systems.
Some solar pumps are still equipped with comparably cheap brushed DC motors. The main disadvantage of brushed motors is that brushes are subject to wear and tear and need to be replaced at regular intervals (approximately every two years). DC motors are mainly used for small to medium-sized irrigation schemes, while AC motors are gaining importance in applications where higher output/head combinations are required. The controller has to have an inverter if the pump is AC. Innovations in DC/AC inverter technology have led to the development of specially designed pump inverters that can drive conventional AC motors. Non-compatible inverter/motor combinations may reduce the expected lifetime of the conventional AC motor. Therefore, well matched and tested controller/motor combinations are recommended to increase system reliability.